Stages in large-scale water treatment
There are often seven steps (Figure 5.2) in large-scale water treatment for urban municipal water supply (Abayneh, 2004). Each of the steps will be described in turn in this section. The water utility (the organisation that runs the treatment plants and water distribution system) will ensure by regular analysis of the water that it adheres to quality standards for safe water. (Water quality standards will be described in Study Session 9.)
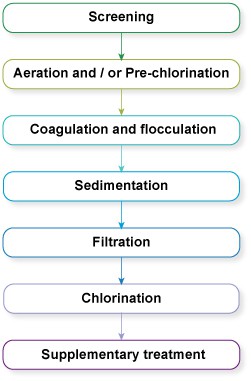
Figure 5.2 The seven steps often used in the large-scale treatment of water.
Screening
To protect the main units of a treatment plant and to aid in their efficient operation, it is necessary to use screens to remove any large floating and suspended solids that are present in the inflow. These materials include leaves, twigs, paper, rags and other debris that could obstruct flow through the plant or damage equipment. There are coarse and fine screens.
Coarse screens (Figure 5.3) are steel bars spaced 5–15 cm apart, which are employed to exclude large materials (such as logs and fish) from entering the treatment plant, as these can damage the mechanical equipment. The screens are made of corrosion-resistant bars and positioned at an angle of 60º to facilitate removal of the collected material by mechanical raking.
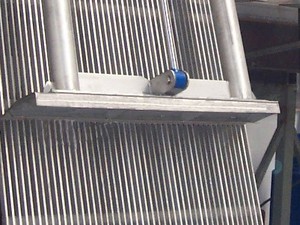
Figure 5.3 A coarse screen.
Fine screens, which come after the coarse screens, keep out material that can block pipework at the plant. They consist of steel bars which are spaced 5–20 mm apart. A variation of the fine screen is the microstrainer (Figure 5.4) which consists of a rotating drum of stainless steel mesh with a very small mesh size (ranging from 15 µm to 64 µm, i.e. 15–64 millionths of a metre). Suspended matter as small as algae and plankton (microscopic organisms that float with the current in water) can be trapped. The trapped solids are dislodged from the fabric by high-pressure water jets using clean water, and carried away for disposal.
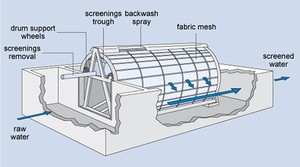
Figure 5.4 Diagram of a microstrainer.
Aeration
After screening, the water is aerated (supplied with air) by passing it over a series of steps so that it takes in oxygen from the air. This helps expel soluble gases such as carbon dioxide and hydrogen sulphide (both of which are acidic, so this process makes the water less corrosive) and also expels any gaseous organic compounds that might give an undesirable taste to the water. Aeration also removes iron or manganese by oxidation of these substances to their insoluble form. Iron and manganese can cause peculiar tastes and can stain clothing. Once in their insoluble forms, these substances can be removed by filtration.
In certain instances excess algae in the raw water can result in algal growth blocking the sand filter further down the treatment process. In such situations, chlorination is used in place of, or in addition to, aeration to kill the algae, and this is termed pre-chlorination. This comes before the main stages in the treatment of the water. (There is a chlorination step at the end of the treatment process, which is normal in most water treatment plants). The pre-chlorination also oxidises taste- and odour-causing compounds.
Coagulation and flocculation
After aeration, coagulation takes place, to remove the fine particles (less than 1 µm in size) that are suspended in the water. In this process, a chemical called a coagulant (with a positive electrical charge) is added to the water, and this neutralises the negative electrical charge of the fine particles. The addition of the coagulant takes place in a rapid mix tank where the coagulant is rapidly dispersed by a high-speed impeller (Figure 5.5).
Since their charges are now neutralised, the fine particles come together, forming soft, fluffy particles called ‘flocs’. (Before the coagulation stage, the particles all have a similar electrical charge and repel each other, rather like the north or south poles of two magnets.) Two coagulants commonly used in the treatment of water are aluminium sulphate and ferric chloride.
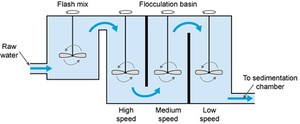
Figure 5.5 The coagulation–flocculation process.
The next step is flocculation. Here the water is gently stirred by paddles in a flocculation basin (Figure 5.5) and the flocs come into contact with each other to form larger flocs.
The flocculation basin often has a number of compartments with decreasing mixing speeds as the water advances through the basin (Figure 5.6(a)). This compartmentalised chamber allows increasingly large flocs to form without being broken apart by the mixing blades. Chemicals called flocculants can be added to enhance the process. Organic polymers called polyelectrolytes can be used as flocculants.
Sedimentation
Once large flocs are formed, they need to be settled out, and this takes place in a process called sedimentation (when the particles fall to the floor of a settling tank). The water (after coagulation and flocculation) is kept in the tank (Figure 5.6(b)) for several hours for sedimentation to take place. The material accumulated at the bottom of the tank is called sludge; this is removed for disposal.
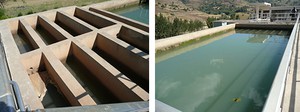
Figure 5.6 Flocculation chambers (a) and a sedimentation tank (b) at Gondar water treatment works.
Filtration
Filtration is the process where solids are separated from a liquid. In water treatment, the solids that are not separated out in the sedimentation tank are removed by passing the water through beds of sand and gravel. Rapid gravity filters (Figure 5.7), with a flow rate of 4–8 cubic metres per square metre of filter surface per hour (this is written as 4–8 m–3 m–2 h–1) are often used.
When the filters are full of trapped solids, they are backwashed. In this process, clean water and air are pumped backwards up the filter to dislodge the trapped impurities, and the water carrying the dirt (referred to as backwash) is pumped into the sewerage system, if there is one. Alternatively, it may be discharged back into the source river after a settlement stage in a sedimentation tank to remove solids.
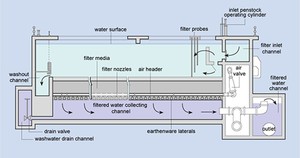
Figure 5.7 Cross-sectional diagram of a rapid gravity sand filter.
Chlorination
After sedimentation, the water is disinfected to eliminate any remaining pathogenic micro-organisms. The most commonly used disinfectant (the chemical used for disinfection) is chlorine, in the form of a liquid (such as sodium hypochlorite, NaOCl) or a gas. It is relatively cheap, and simple to use. When chlorine is added to water it reacts with any pollutants present, including micro-organisms, over a given period of time, referred to as the contact time. The amount of chlorine left after this is called residual chlorine. This stays in the water all the way through the distribution system, protecting it from any micro-organisms that might enter it, until the water reaches the consumers.
World Health Organization Guidelines (WHO, 2003) suggest a maximum residual chlorine of 5 mg l–1 of water. The minimum residual chlorine level should be 0.5 mg l–1 of water after 30 minutes’ contact time (WHO, n.d.). There are other ways of disinfecting water (e.g. by using the gas ozone, or ultraviolet radiation) but these do not protect it from microbial contamination after it has left the water treatment plant. Following disinfection the treated water is pumped into the distribution system.
Supplementary treatment
Supplementary treatment may sometimes be needed for the benefit of the population. One such instance is the fluoridation of water, where fluoride is added to water. It has been stated by the World Health Organization that ‘fluoridation of water supplies, where possible, is the most effective public health measure for the prevention of dental decay’ (WHO, 2001). The optimum level of fluoride is said to be around 1 mg per litre of water (1 mg l–1).
On the other hand, as you learned in Study Session 2, in the Rift Valley of Ethiopia, the water resources contain a higher concentration of fluoride than is desirable. Tekle-Haimanot et al. (1995) found that the level of fluoride in drinking water from deep wells there ranged from 1.5 to 36 mg l–1. The safe level for fluoride is 1.5 mg l–1.
What does excess fluoride in the water lead to?
As mentioned in Study Session 2, in children it can cause mottling of teeth and prolonged exposure can cause skeletal fluorosis and crippling.
In such high-fluoride areas, removal or reduction of fluoride (termed defluoridation) is essential. The simplest way of doing this is to blend the high-fluoride water with water that has no (or very little) fluoride so that the final mixture is safe. If this is not possible, technical solutions may be applied. Two of these, the Nakuru Method and the Nalgonda Technique, used in Ethiopia, are described below.
The Nakuru Method (Figure 5.8) involves a filter with bone char (charcoal produced from animal bone) and calcium phosphate to adsorb the fluoride (Kung, 2011). There have been reservations on the use of bone char, and alternatives for defluoridation, such as activated alumina, are being tested in Addis Ababa (Alemseged, 2015).
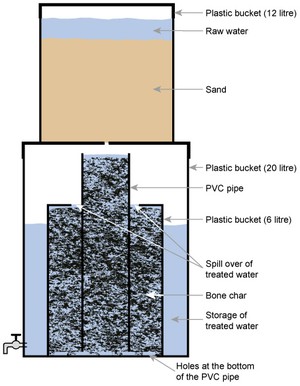
Figure 5.8 The Nakuru method for defluoridation using plastic buckets and piping.
The Nalgonda technique for defluoridation (Suneetha et al., 2008) uses aluminium sulphate and calcium oxide to remove fluoride. The two chemicals are added to and rapidly mixed with the fluoride-contaminated water and then the water is stirred gently. Flocs of aluminium hydroxide form and these remove the fluoride by adsorption and ion exchange. The flocs are then removed by sedimentation.